6 Equipment Preventive Maintenance Tips
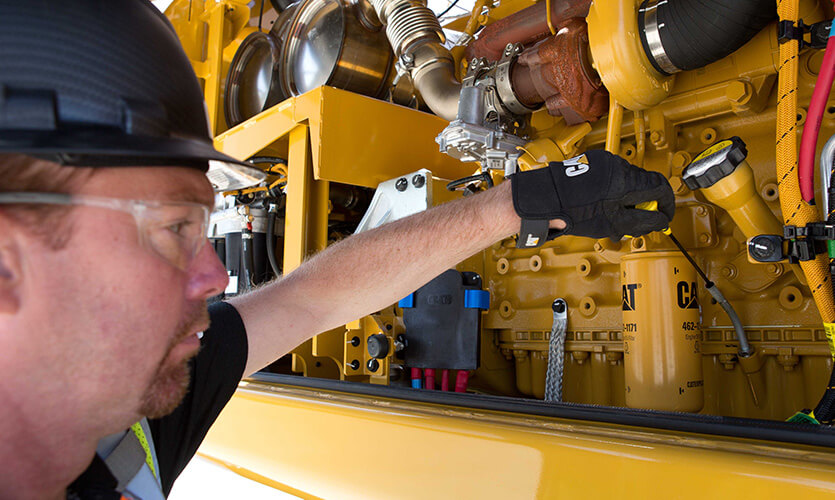
Heavy machinery is essential for your business, and you want to ensure your equipment will last as long as possible while performing at peak efficiency. Regular maintenance can help keep your equipment running smoothly and reduce costly, unexpected repairs and downtime.
Performing preventive maintenance requires careful planning and adequately trained technicians. Learn more about preventive maintenance, why it’s essential for your business and the steps to perform maintenance properly.
Jump To Sections:
- What Is Construction Equipment Maintenance?
- What Is the Importance of Preventive Maintenance?
- Why Use a Heavy Equipment Preventative Maintenance Program?
- Steps for Preventive Maintenance
- Heavy Equipment Maintenance Checklist
- Contact Warren CAT To Learn More
What Is Construction Equipment Maintenance?
Construction or heavy equipment maintenance refers to the service and steps you take to identify, repair or prevent machinery problems. Equipment maintenance typically involves inspecting, repairing and cleaning your machinery.
Maintenance can be split into two separate categories:
- Preventive maintenance: This type of maintenance involves scheduled tasks that help prevent issues from occurring and keeps your equipment running at its optimal performance. Common types of preventive maintenance include oil, grease, coolant and other fluid changes; belt, hose and filter replacement; pressure checks and routine cleanings.
- Reactive maintenance: This type of maintenance happens after a problem has occurred, usually when equipment stops operating as it should or fails completely. Reactive maintenance only addresses problems when they become apparent, with little opportunity for planning and increased cost and inconvenience.
Ideally, you should conduct preventive maintenance regularly to reduce the need for reactive maintenance, ensuring your heavy equipment operates correctly and extends its life span.
What Is the Importance of Preventive Maintenance?
Preventive maintenance is one of the most important things you can do for your company’s heavy equipment. Preventive maintenance can provide value and numerous benefits to your company and equipment, including:
- Reduced expenses: Preventive maintenance helps reduce the risk of unexpected failures or breakdowns that can incur expensive repairs. Performing maintenance regularly can decrease the severity of problems and reduces the risk of compound failures, which can quickly become a significant issue and rack up costs.
- Extended life spans: Preventive maintenance ensures your machinery is in the best condition possible, which can help extend the life of your equipment. Regularly maintained machinery lasts longer than equipment that doesn’t undergo regular maintenance. Longer life spans significantly benefit your company since you can reduce downtime, increase productivity and save on expensive repairs or replacements.
- Improved safety: Well-maintained equipment is safer than equipment that’s not maintained. If equipment fails unexpectedly, it can create a hazardous environment for the operator, nearby workers and surrounding property. Regular maintenance helps you identify and address any potential hazards before they become a significant problem.
- Greater confidence: Heavy equipment operators feel more confident working with regularly maintained machinery since they know it’s more likely to work efficiently and effectively. If operators are concerned that their equipment will break, they’ll likely slow down their work. Preventive maintenance can give your operators more confidence to work with equipment and optimize productivity.
- More availability: You can’t use broken-down equipment, harming productivity and profits while you wait for repairs or replacements. Preventive maintenance ensures that your heavy machinery is more available for your jobs, allowing you to complete tasks on time.
Why Use a Heavy Equipment Preventative Maintenance Program
A preventative maintenance program can help you maintain your equipment’s maintenance requirements, including performance testing, equipment analysis, systematic inspections and component replacements. Trying to perform preventive maintenance without a maintenance program can create problems, such as forgetting to stay on schedule, overlooking essential maintenance requirements or failing to keep track of prior maintenance.
A proper preventative maintenance program will be all-inclusive, making it an intentional approach to equipment maintenance from the first hour logged through its entire lifespan. Preventative maintenance programs can include the following:
- Failure analysis
- Site inspections
- Fluid Analysis
- In-shop servicing
- Diagnostic technology
- Machine inspection data collection
- Total maintenance and repair agreements
- Training and safety videos for operators and workers
Some programs will be more complex than others depending on the type of machinery. Regardless of the equipment type, preventative maintenance programs can help improve a machine’s performance, reliability, safety, productivity and lifespan.
Steps for Preventive Maintenance
Following the appropriate steps or tips for preventive maintenance ensure you care for your equipment properly and help it last a long time. Steps for your preventive maintenance include the following:
1. Schedule Your Preventive Maintenance
Creating a schedule for your preventive maintenance is the first step to ensuring your machinery operates at peak performance and doesn’t experience unexpected failures. A company schedule helps you remember to perform maintenance, informs your team when they need to be maintaining your equipment and allows for planning around your production schedule. The manufacturer’s recommendations should serve as your guidelines for planning and scheduling maintenance.
2. Keep Documentation of Services and Repairs
Keep documentation every time you perform maintenance. Knowing what repairs and services you’ve done helps you know which repairs you need to do soon. A history of repairs and services can help you determine if your equipment is excessively impacting your bottom line and also help your fleet maintain its value.
3. Use Checklists
Checklists can help ensure that workers follow the proper maintenance steps and meet the requirements during each inspection. They guide operators and technicians through the process of evaluating and performing maintenance. As each step is completed, workers can check off what they’ve done to track what they need to do next. Checklists can cover everything from visual inspections to equipment operations.
4. Clean Regularly
Another step you’ll want to take is cleaning your heavy equipment regularly. Cleaning helps your technicians check for issues or signs of damage that must be addressed. Workers should be trained to spot damage while they’re cleaning your equipment.
Cleaning is also a form of heavy equipment maintenance. Dirt and other contaminants can prevent moving parts from operating correctly, which can cause damage or failures. Cleaning regularly can prevent these problems before they compound into something more serious.
5. Customize Maintenance and Service Based on Machine Type
You likely use various types of equipment within your company for multiple applications. Different machines need various types of maintenance and service. Rather than using a one-size-fits-all maintenance plan, you should create specific maintenance requirements for each machine type to ensure each piece of equipment works efficiently. Follow the manufacturers’ recommendations for the maintenance and service of each machine.
6. Train Operators on Machine Use
Operators who know how to use the equipment correctly will be less likely to cause damage or push machinery past its limits. Proper training reduces the risk of needing additional maintenance to fix this damage, abuse or overuse. Training can also include identifying maintenance issues, which can help keep each machine in your fleet in optimal health.
Heavy Equipment Maintenance Checklist
As we mentioned, creating a checklist for your maintenance is an excellent way to track the tasks you’ve performed and what you still need to do. These checklists remind technicians what is required and when. Some common tasks or places technicians should check that you can include on your checklist include:
- Batteries
- Bearings
- Belts
- Brakes
- Coolant and other fluids
- Electrical components
- Filters
- Fuel
- Idlers, sprockets and other rotating components
- Oil, grease and other lubricants
- Steering systems
- Safety devices
- Teeth, tips, blades, edges, wear plates and other ground engaging tools
- Wheels, tires and tracks
- Windshields and glass
As your technicians perform maintenance, they can check off each task. The checklist provides guidelines rather than instructions on how to complete maintenance. Technicians will still need the training to properly perform the appropriate level of maintenance for each type of machinery your company owns.
Learn More About Warren CAT’s Preventive Maintenance Kits in Oklahoma and West Texas
Performing preventive maintenance can help save you time and money while keeping your equipment running smoothly for years. Warren CAT is the authorized Cat® dealer for West Texas and the state of Oklahoma that sells preventative planned maintenance kits to make it easier to stay on track with routine maintenance. Our kits are customized to fit your machinery, ensuring you have everything you need to keep your heavy equipment fleet’s maintenance on track.
Our kits help remove the guesswork, so you have less to worry about. The Warren CAT team of experts can help you find exactly what you need and will guide you through each step of the process. Contact us today to learn more about our preventative maintenance kits and how we can help!